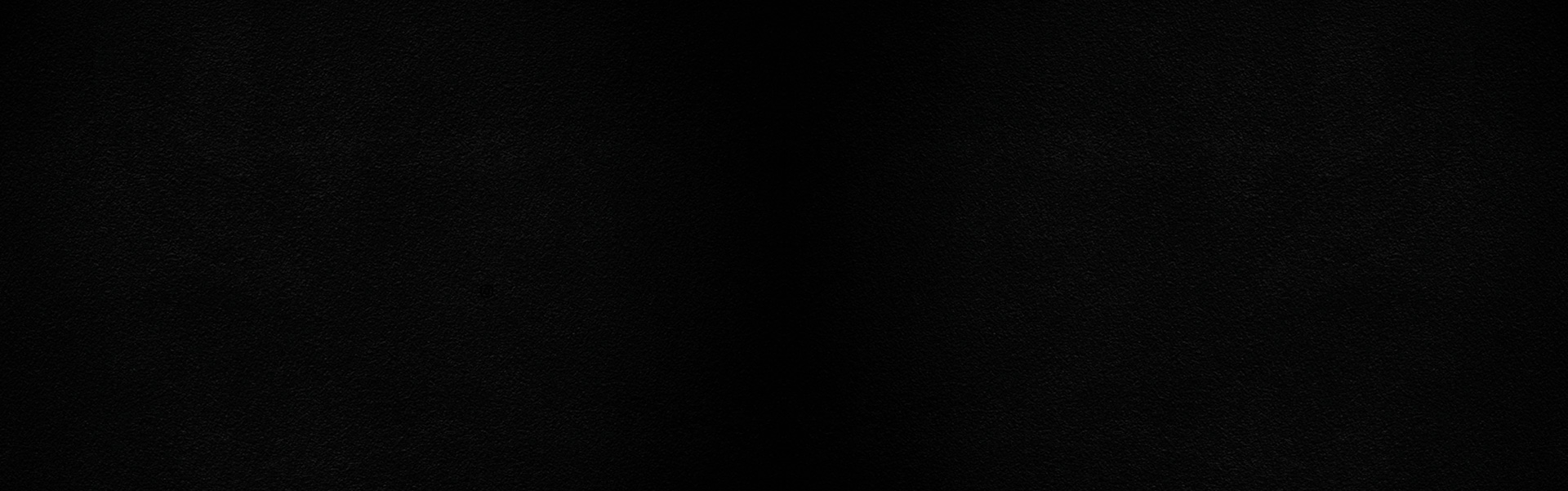
Unit 7B, 30-32 Barcoo Street, Roseville NSW 2069
Unit 7B, 30-32 Barcoo Street, Roseville NSW 2069
Polished concrete is strong, durable and low maintenance while having that down-to-earth quality of stone with a polish equal to granite. It is comparable to traditional polished terrazzo which is very flat and poured as a special mix to make the finish more successful. Polished concrete floors can also look almost bumpy and have little or no aggregate showing.
Flatness, levelness and polishing are not necessarily the same thing. It costs extra time and diamond wear to cut floors with a concrete grinder until they are flat. They can either be ground flat to fully expose the aggregate like terrazzo, the aggregate can be partially exposed, or the concrete grinding can expose no more than the fine sands at the surface (usually called salt and pepper). It often takes skill and experience to control the process of polished concrete floors and the quality of the concreter’s original finishing work is a large factor in the quality of the finish. Where the aggregate is the main feature, special supplies can be added to the wet concrete mix such as colored pebbles, metals and glass to enhance the final look. Most people are unaware that there can be seven to ten steps for polished concrete floors which takes a long time to complete and can be quite expensive. Normally it takes many polishing passes to finish a highly polished floor although there are other ways as explained later. The general rule is to double the diamond grit size under the concrete polisher for each pass so a service provider might start with very coarse, 16 or 32 grit size diamonds, then use 60 grit diamonds followed by 120, then start again with a 50 grit diamond resin pad instead of a metal segment. Using the resin pads the steps may be 100, then 200, 400, 800, 1500 and finally 3000 grit. That would be ten separate grinding passes which does not count the two other essential steps.
Two more essential steps:
Simple polished concrete floors “look”
The number of processes for polishing concrete can be reduced by up to 60% and still achieve a similar appearance by grinding and then coating with a clear penetrating sealer. Starting with a 100 grit resin bond diamond the proceeding up through the 400 grit resin bond the floor is ready for these newly introduced polymer wonders. The penetrating sealer is applied and then burnished to an ultra high sheen thus saving the customer quite a bit of money. This process is being used in supermarkets, home improvement stores, restaurant and many big box locations including the big discount membership stores.
In the case of the customer wanting a coating but still the look: The first step is to grind with 30/40 grit diamonds to expose the aggregate, then fill all the small air holes as described above (in 10 to 15 steps) before a second grind with 60/80 grit or 80/100 grit diamonds. This will produce a smooth enough surface to coat with a sealer. Polyurethanes are very hard sealers with a high gloss and can be purchased as UV stable to stop yellowing (usually double the price of non UV stable urethanes), clear epoxy sealers are not as smooth and will chalk and deteriorate if exposed to sunlight and acrylic sealers have a much shorter lifespan due to their poor resistance to wear. Two coats are necessary to provide a high gloss level.
Single head or multiple head machines:
Originally terrazzo grinding was done with single head floor grinders until the production of three-head
planetary machines. Planetary means that each head turns one direction while the turntable that houses the heads turns independently in either the same direction or the opposite direction. Some grinders can
vary the direction of both the turntable and the heads and some can vary the speed of each. There are also multiple head planetary machines with four or more heads. Each of these machines has its own
advantages and disadvantages. The planetary heads can follow the contours better than single or twin head grinders and are faster to use with less effort due to eliminating the requirement to physically move the grinder from side to side or in a circular motion.
Assorted ways to achieve “polished concrete”
The first is to grind the floor with coarse diamonds until all the high spots have been removed to produce
a flat floor and then use all of the 12 to 15 steps to eventually polish it or as it is sometimes called, hone
it. To hone the floor is to only take it to the 200-400 grit resin level. This is the true polishing system.
A variation of the above is to cut perhaps half of the height of the higher peaks by starting with a
medium coarse diamond grit and proceed through to polishing using a machine that can ride up and
over small rises.
A third alternative way of producing a honed surface is to start with relatively fine diamonds and simply polish to top of the surface after hardening without removing much of the top cement paste. It is easier to do this when the floor has been laid flat and smooth. Lastly, a “polished look” can be obtained by grinding with coarse diamonds and then fine diamonds before coating over with a clear sealer.
It is true that only truly polished floors will retain their gloss with little maintenance because all coatings
scratch with wear and lose their high shine. Special polishing pads on a standard floor polisher that
contain very fine diamonds can be used to maintain sanitation and the high gloss levels of true polished concrete. Janitors can be provided with these and keep the floors in great condition without special handling.
Some rental companies provide the polishing equipment for do-it-yourself concrete polishing and have all the pads for the purpose. This may not be so economical though because the pads may be only
half worn when you finish depending on the area involved. It also takes a bit of skill and experience to
know what to do to achieve a high quality floor. This experience is usually passed down from a
quality skilled contractor or teacher in the work environment.